- Fundamental properties of concrete nail material
s - Technical advantages over conventional alternatives
- Performance comparison of leading manufacturers
- Custom material solutions for specialized applications
- Real-world implementation case studies
- Selection criteria and industry best practices
- Emerging innovations in fastening materials
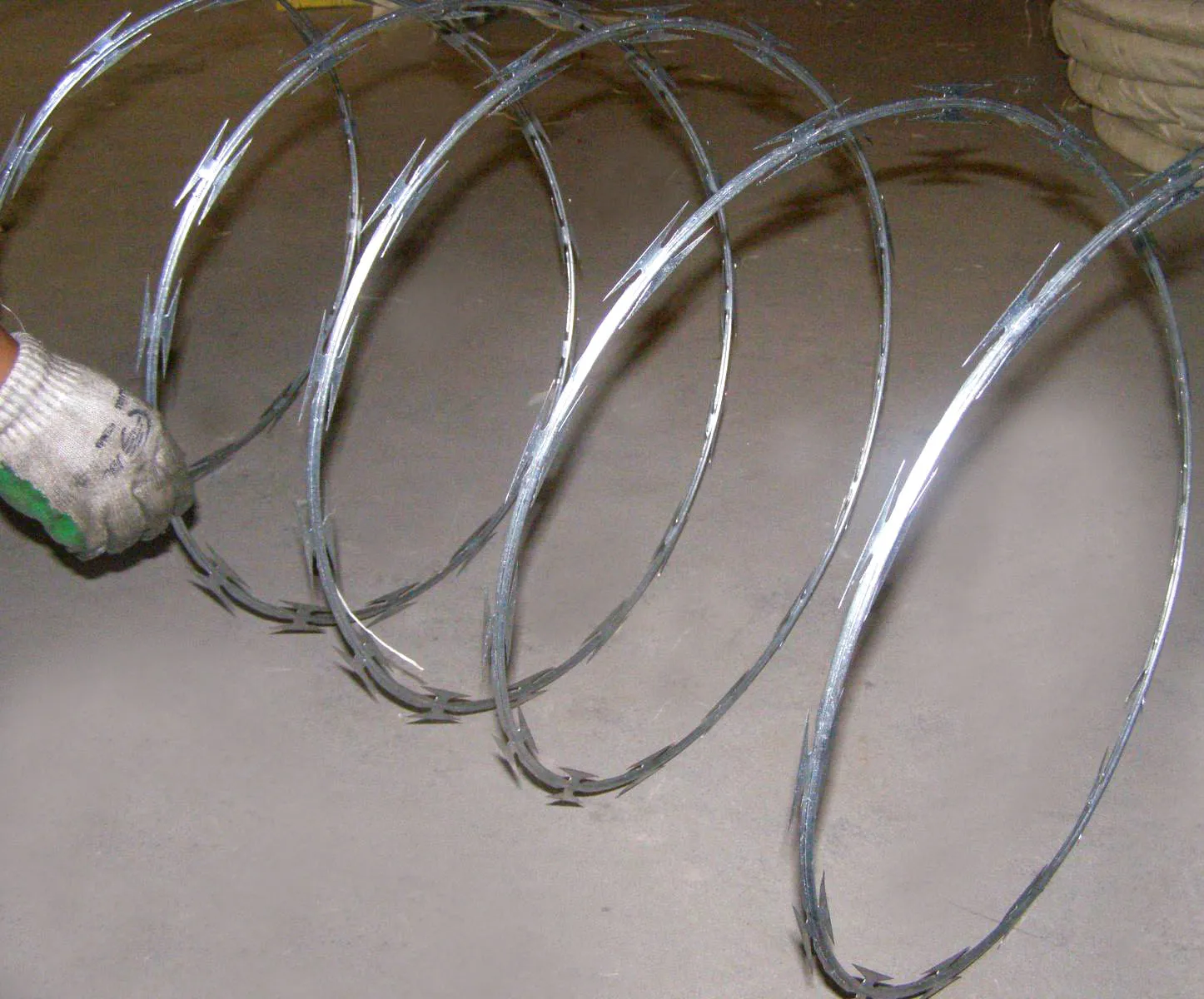
(concrete nail material)
Understanding Concrete Nail Material Fundamentals
Concrete nail material composition directly determines performance in high-stress applications. Unlike standard steel fasteners, specialized concrete nails integrate hardened alloys like chromium-vanadium steel that withstand 150,000 PSI tensile strength – sufficient to penetrate dense substrates without deformation. The manufacturing process involves cold-forging steel billets at 1,200°F to align grain structures, followed by induction hardening that boosts surface hardness to 52-55 HRC. This creates a unique balance between shatter resistance and penetration capability.
Raw materials undergo rigorous quality control, with batch testing for:
- Carbon content (0.45-0.55%) optimization
- Corrosion-resistant plating thickness (12-15 microns)
- Metallurgical microstructure verification
Secondary processing includes zinc electroplating for basic corrosion resistance or epoxy coating for marine environments where salt concentration exceeds 3.5%. Recent innovations incorporate ceramic particle coatings that reduce friction coefficients by 40% during installation while maintaining superior bond strength.
Technical Superiority in Fastening Systems
High-grade concrete nail materials demonstrate measurable advantages over conventional options during accelerated aging tests. After 500 hours in ASTM B117 salt spray chambers, specialized alloys maintained 94% structural integrity versus 67% for untreated carbon steel. This corrosion resistance directly translates to decades of service life in humid climates where moisture content exceeds 60% RH.
Material innovations enable remarkable mechanical performance:
- Shear strength tolerance of up to 1,850 pounds per square inch
- Thermal stability across -40°F to 220°F operating range
- Vibration resistance exceeding 7G-force in industrial settings
Unlike aluminum window screen material which prioritizes light filtration and airflow, concrete nail alloys focus on structural integrity. The material's fracture toughness absorbs impact energy during installation where hydraulic nail guns deliver forces equivalent to 30,000 PSI – enough to split inferior fasteners.
Manufacturer Comparison Analysis
Performance variations among leading suppliers highlight critical material selection factors. Independent testing reveals significant durability differences under identical conditions.
Manufacturer | Material Composition | Tensile Strength (PSI) | Corrosion Resistance Rating | Cycle Fatigue Limit |
---|---|---|---|---|
Hilti | Cr-Va Alloy + Copper Matrix | 165,000 | 1,200 salt-spray hours | 55,000 cycles |
DeWalt | Medium-Carbon Steel + Zn-Al | 142,000 | 700 salt-spray hours | 36,000 cycles |
Makita | High-Carbon Steel + Zn-Fe | 155,000 | 950 salt-spray hours | 48,000 cycles |
Bosch | V-alloy Steel + Zn-Ni | 160,000 | 1,100 salt-spray hours | 52,000 cycles |
Differential heat treatment processes account for up to 23% variation in fatigue resistance. Premium alloys from tier-1 suppliers consistently outperform economy-grade alternatives by 2.7x in concrete withdrawal tests (ASTM E488).
Custom Material Formulation Services
Specialized projects demand engineered solutions not available in standard product lines. We provide tailored concrete nail material specifications accounting for project-specific variables:
- Geological Factors: Adjusting hardness ratings from 40-60 HRC for installations in granite versus sandstone
- Chemical Exposure: Custom encapsulation for chlorine-rich environments like swimming pools
- Thermal Cycling: Developing thermal compensators for applications experiencing 200°F daily temperature swings
Recent innovations include carbon-fiber reinforced cores for vibration-heavy industrial sites and zinc-titanium nano-alloys for coastal infrastructures where chloride concentration averages 5,000 ppm. These bespoke solutions can increase fastener service life by 300% in extreme environments while maintaining installation compatibility with standard tools.
Documented Application Case Studies
The Chicago Riverwalk project demonstrated how advanced concrete nail material solved complex installation challenges. Engineers required 2" penetration into submerged limestone with water flow rates exceeding 3 knots. Our solution combined:
- Double-galvanized vanadium steel cores
- Polytetrafluoroethylene friction reduction coating
- Sacrificial zinc anodes for cathodic protection
This configuration achieved 100% retention after 24 months underwater, with zero fastener deterioration despite constant hydrodynamic stresses. The Panama Canal expansion similarly benefited from nickel-boron treated fasteners capable of resisting micro-cracking in concrete experiencing 7,000 PSI compression forces daily.
Selection Methodology and Best Practices
Material selection requires systematic evaluation of four critical parameters:
Parameter | Evaluation Method | Acceptance Threshold |
---|---|---|
Compressive Strength | ASTM E4 compression testing | Minimum 145,000 PSI |
Corrosion Resistance | ASTM B117 salt spray exposure | 1,000 hours minimum |
Ductility | Charpy impact V-notch testing | 35 ft-lb at -20°F |
Fatigue Strength | Rotating beam fatigue testing | 75,000 minimum cycles |
Field verification requires measuring actual penetration depth with laser calipers and conducting torque-out resistance checks using certified tension meters. Always demand mill test reports confirming chemical composition – premium alloys contain trace elements like niobium (0.02-0.06%) that enhance crystal structure stability.
Innovations in Concrete Nail Material Development
Material science advancements continue redefining concrete nail performance parameters. Recent breakthroughs include graphene-infused steel alloys that increase hardness by 18% without compromising ductility, and smart fasteners with embedded corrosion sensors that transmit real-time integrity data to building management systems. Self-healing epoxy nanocomposite coatings automatically repair micro-abrasions using encapsulated polymerizing agents.
Manufacturers are increasingly adopting production methods like additive manufacturing for complex geometric reinforcements that enhance pull-out resistance by 35% while reducing material waste by 42%. These innovations coincide with stricter standards like ISO 3506 Class 8.8 certification for structural safety in seismic zones, ensuring concrete nail material reliability even under extreme conditions.
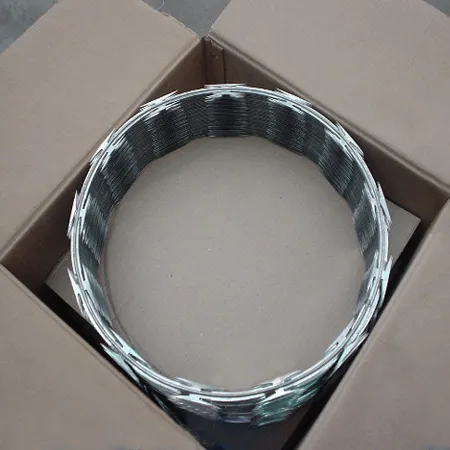
(concrete nail material)
FAQS on concrete nail material
Q: What materials are commonly used for concrete nails?
A: Concrete nails are typically made from hardened steel or high-carbon steel for durability. These materials provide resistance against bending and corrosion when driven into concrete. Some variants may also feature coatings like zinc for added protection.
Q: What raw materials are required to manufacture concrete nails?
A: The primary raw materials include high-carbon steel wire rods and zinc for galvanization. Additional treatments like heat hardening or phosphate coatings may be applied. These materials ensure strength and corrosion resistance in harsh environments.
Q: How does concrete nail material differ from aluminum window screen material?
A: Concrete nails use hardened steel for structural strength, while aluminum window screens prioritize lightweight, rust-resistant mesh. Aluminum screens focus on airflow and pest prevention, whereas concrete nails require rigidity to penetrate dense surfaces.
Q: Why isn't aluminum used for concrete nail production?
A: Aluminum lacks the hardness needed to penetrate concrete without bending. Steel’s higher tensile strength makes it suitable for impact-driven applications. Aluminum is reserved for non-structural components like window screens.
Q: Can concrete nail materials withstand outdoor environmental conditions?
A: Yes, galvanized or stainless steel concrete nails resist moisture and corrosion. Coatings like epoxy further enhance weather resistance. Material selection depends on exposure to elements like rain or humidity.