Welded Wire Fabric in Concrete Reinforcement
Welded wire fabric (WWF) is a critical component in modern concrete reinforcement, playing an essential role in enhancing the structural integrity of concrete structures. This prefabricated steel mesh is composed of longitudinal and transverse wires that are welded together at their intersections, creating a grid-like pattern. The use of welded wire fabric has become increasingly popular in the construction industry due to its numerous advantages over traditional reinforcement methods.
Advantages of Welded Wire Fabric
One of the primary benefits of welded wire fabric is its strength. The welded intersections provide a consistent and reliable reinforcement throughout the concrete, significantly improving its load-bearing capacity. The use of WWF allows for uniform distribution of stress, reducing the risk of cracking and structural failure. This is particularly important in applications where the concrete is subjected to dynamic loads, such as in pavements, bridges, and slabs.
WWF is also known for its ease of installation. The mesh sheets can be pre-cut to size and laid out quickly on site, which can significantly speed up the construction process. Unlike rebar, which requires bending and tying, welded wire fabric can be placed more efficiently, saving time and labor costs. This streamlined installation process is particularly advantageous in large-scale construction projects, where efficiency is crucial.
Moreover, the use of welded wire fabric can lead to reduced material costs. The standardized sizes and shapes of the fabric allow for more optimal use of materials, minimizing waste. Additionally, the overall weight of the welded wire fabric is less than that of traditional rebar placement when considering equivalent strengths, which can result in transportation and handling cost savings.
Types of Welded Wire Fabric
welded wire fabric concrete reinforcement
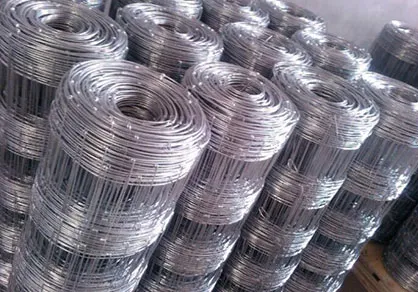
Welded wire fabric comes in various types and grades, designed to meet specific requirements of different construction projects. The most common types include plain and deformed wire fabric. Plain wire fabric offers smooth surfaces, while deformed wire fabric features ridges that improve bond strength with concrete. The selection of the appropriate type depends on the structural requirements and the specific characteristics of the concrete mix being used.
Applications of Welded Wire Fabric
Welded wire fabric is employed in a wide range of applications. It is widely used in residential, commercial, and industrial concrete slabs, allowing for enhanced durability and strength. In pavements, WWF helps in mitigating cracking caused by shifting and settling, thus extending the lifespan of road surfaces. In precast concrete elements, such as beams and panels, welded wire fabric provides added reinforcement, which is crucial during transport and handling.
Additionally, WWF is increasingly used in residential applications, such as in concrete driveways and patios, providing a solid framework that helps resist cracking. The versatility of welded wire fabric makes it suitable for various structural scenarios, enhancing performance while maintaining cost-effectiveness.
Conclusion
In summary, welded wire fabric is a vital innovation in concrete reinforcement that offers significant benefits over traditional methods. Its strength, ease of installation, and cost-effectiveness make it a preferred choice in the construction industry. As the demand for robust and durable concrete structures continues to grow, the use of welded wire fabric will likely become even more prevalent. Understanding its applications and advantages is essential for engineers, architects, and contractors aiming to optimize their construction practices and deliver high-quality structures that stand the test of time.