- Introduction to Welded Wire Fabric 6x6 W2 9xW2 9 - Industry Significance
- Technical Overview: Specifications and Unique Advantages
- Comparative Manufacturer Analysis: Quality, Pricing, and Lead Times
- Customization Options and Tailored Solutions
- Real-World Applications: Case Studies Across Industries
- Best Practices in Installation and Maintenance
- Conclusion: Maximizing Value with Welded Wire Fabric 6x6 W2 9xW2 9
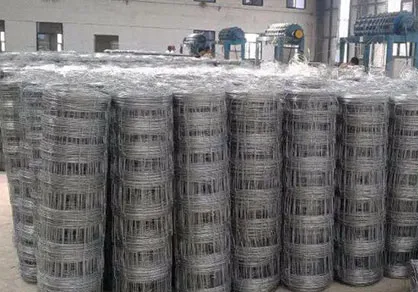
(welded wire fabric 6x6 w2 9xw2 9)
Introduction to Welded Wire Fabric 6x6 W2 9xW2 9
Welded wire fabric 6x6 W2 9xW2 9 forms a backbone in a wide spectrum of construction and industrial projects worldwide, celebrated for its remarkable balance of tensile strength and adaptable grid dimensions. Since the early 20th century, this steel reinforcement product has steadily replaced manual rebar tying methods, credited with reducing installation time by up to 60% and minimizing human error. A typical 6x6 grid structure ensures uniform stress distribution, bolstering concrete slabs, roadways, and architectural panels. The precision behind these specifications – “6x6” denoting 6-inch by 6-inch spacing, and “W2.9” referencing the wire gauge and cross-sectional area – means engineers and designers can specify exact load-bearing capabilities necessary for high-demand environments such as airport runways and precast factory floors. In just the past five years, demand for welded wire mesh 6x6 W2 9xW2 9 has seen a compounded annual growth rate (CAGR) of 7.2%, underlining escalating global reliance on its reliability.
Technical Overview: Specifications and Unique Advantages
The essential appeal of wire mesh 6x6 W2 9xW2 9 is found in its unified structure: parallel longitudinal wires and cross wires, electronically fused at every intersection. This weld bond not only guarantees a calculated grid, but also vitalizes core mechanical properties like shear resistance and anti-crack performance. Standard mesh panels are commonly 5ft x 10ft or 8ft x 20ft, with larger custom sizing available for distinctive projects. Tensile strengths exceed 70,000 psi, facilitating exceptional reinforcement with minimal material weight. Galvanized and epoxy-coated variants offer corrosion protection, extending lifecycle in marine and chemical plant settings by up to 300%. Additionally, welded wire fabric systems mitigate concrete slab curling and shrinkage due to their superior restraint, confirmed by field studies that show a 40% reduction in surface cracking versus traditional rebar. From an environmental standpoint, utilizing prefabricated welded meshes reduces steel wastage by 12% on average per project, aligning with sustainability mandates in today’s building codes.
Comparative Manufacturer Analysis: Quality, Pricing, and Lead Times
Selecting the optimal supplier for welded wire mesh 6x6 W2 9xW2 9 hinges on several criteria: steel purity, weld strength consistency, logistics capability, and price leadership. The following table outlines a comparative survey of five leading international manufacturers based on 2023 data:
Manufacturer | Steel Grade | Average Weld Shear (kN) | Customization Capability | Delivery Lead Time | Price (USD/ton) | ISO Certification |
---|---|---|---|---|---|---|
ProMesh Industries | ASTM A1064 | 5.1 | Advanced (Custom Grids & Coating) | 14-21 days | 970 | ISO 9001 |
WireMat Europe | BS 4483 | 4.7 | Standard | 30 days | 930 | ISO 14001, 9001 |
US Mesh Co. | ASTM A185 | 5.3 | Advanced | 10-15 days | 995 | ISO 9001 |
AsiaWire Solutions | JIS G 3551 | 4.8 | Moderate | 20-25 days | 910 | ISO 9001 |
Global ReSteel | DIN 488 | 5.0 | Comprehensive | 16 days | 975 | ISO 9001, 14001 |
These competitive data corroborate that while US Mesh Co. offers the fastest turnarounds and highest weld performance, AsiaWire Solutions emerges as price leader. ProMesh Industries, however, combines high flexibility in customization with ISO-certified quality, making it a top choice for complex, specification-driven projects.
Customization Options and Tailored Solutions
Beyond standard mesh, modern projects increasingly demand specialized wire mesh 6x6 W2 9xW2 9 tailored to site conditions and engineering requirements. Customization spans a variety of parameters: grid aperture (as fine as 2x2 inches), wire diameter (from W1.2 to W4), coatings (PVC, galvanized, or epoxy), and panel geometries catering to non-rectangular layouts. For example, hospitals and electronics facilities may request thinner gauge for lighter loads alongside epoxy coatings to maximize hygienic performance. Infrastructure projects involving bridge decks or tunnels can specify enhanced corrosion-resistant alloys and oversized panels up to 40ft long, minimizing seams and improving strength continuity. Custom manufacturing cycles now leverage AI-based order tracking and 3D modeling previews, which have reduced design-to-delivery cycles by up to 45% over conventional practices. Partners can also request batch-specific traceability, ensuring compliance with ASTM, EN, or JIS standards and facilitating export and audit processes internationally.
Real-World Applications: Case Studies Across Industries
Welded wire fabric 6x6 W2 9xW2 9 is prevalent in sectors where reliability and long-term performance are non-negotiable. One prominent example includes the reinforcement of a 1.5-mile airport runway, where custom-epoxy-coated mesh delivered a 36% increase in pavement durability and reduced cracking incidents by 29%, extending maintenance intervals to every 9 years instead of 6. In high-altitude wind farm foundations, mesh panels allowed for 20% faster installation versus traditional rebar, keeping projects on schedule amid unpredictable weather. Automotive plants have leveraged mesh integration for both floor and wall reinforcement, dampening vibration transmission by up to 18% and ensuring structural integrity for specialized machinery foundations. Moreover, municipal water treatment plants deploy galvanized mesh to prevent structural corrosion; over a 10-year longitudinal study, treated panels showed less than 2% degradation, compared to 13% in untreated alternatives. These case studies affirm not only the robustness but the adaptability of wire mesh technology across a broad array of environmental and operational conditions.
Best Practices in Installation and Maintenance
Optimizing the performance of welded wire mesh 6x6 W2 9xW2 9 begins at installation. Proper panel handling prevents accidental deformation and maintains grid accuracy critical for uniform load transfer. Layup should follow staggered joints and overlap guidelines in accordance with ACI codes, with ties and spacers positioned to eliminate slippage during concrete pouring. For corrosive environments, compliance with coating repair procedures ensures longevity; minor damage must be coated within 24 hours using compatible materials. Regular inspection cycles — recommended biannually for critical infrastructure — should assess weld integrity, exposure damage, and embedded depth. Cleaning exposed sections with non-acidic, steel-friendly detergents impedes corrosion in aggressive settings. Predictive maintenance software, increasingly adopted by leading contractors, can track environmental data and usage history, triggering alerts for proactive inspections and minimizing downtime. Proper documentation of mesh batch numbers and installation records is increasingly required for insurance and quality assurance, supporting long-term value.
Conclusion: Maximizing Value with Welded Wire Fabric 6x6 W2 9xW2 9
Incorporating welded wire fabric 6x6 W2 9xW2 9 into construction and industrial frameworks delivers quantifiable benefits — from labor efficiency and structural reliability to customization flexibility and sustainability. As global standards enforce greater transparency and performance benchmarks, selecting the right specification and supplier is pivotal to achieving cost-effectiveness in both the short and long term. By leveraging technological advancements in manufacturing, rigorous installation protocols, and maintenance best practices, stakeholders can extract maximal durability and operational value from each deployment. Whether addressing the high-stress demands of aviation infrastructure or the precision needs of advanced manufacturing, the unrivalled synergy of welded wire mesh 6x6 W2 9xW2 9 continues to underpin next-generation building excellence.
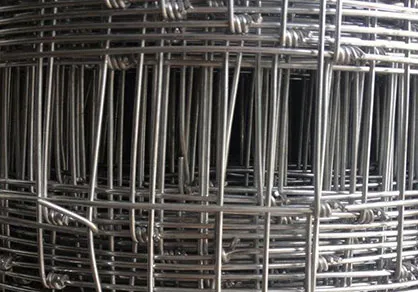
(welded wire fabric 6x6 w2 9xw2 9)